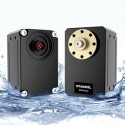
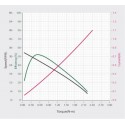
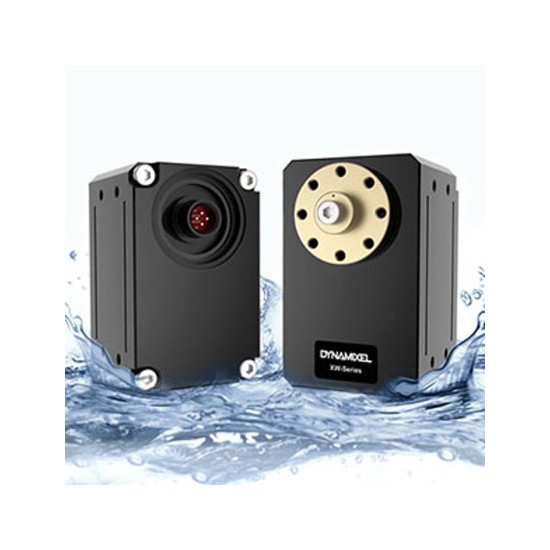
Get a quote in only 3 steps!
1. Add the items you are interested in to your cart
2.Go to your cart
3.Click on GENERATE A QUOTE
Tous vos devis sont accessibles à partir de votre compte client.
The Dynamixel XW430-T200-R actuator with RS485 connection combines a 100% waterproof device with a medium torque, allowing for some speed if required.
Check that your Dynamixel servomotor is correctly configured. Do not hesitate to re-flash it with the ROBOTIS Software Roboplus. After re-flash remember to re-configure it. If the issue is not solved, contact us for an advanced support.
The motor is probably not well mounted. Check that you correctly mounted the horns by respecting the mark.
There is probably a mechanical issue with the Dynamixel servomotor. You can directly contact us to get more advance support.
Check your power supply and the system cabling (try with a different servomotor). You can also reset the servo. If nothing works, the best solution is to go through the Dynamixel servomotor checklist!
The 1.0 protocol is dedicated to the Dynamixel AX and MX series. Protocol 2.0 is for the X and Dynamixel Pro series. Protocol 2.0 control tables include PID controls which allow for more precise adjustment of the servo motor movements. Protocol 2.0 can be updated on MX series servo motors. You can refer to the protocol 1.0 and protocol 2.0 pages for more informations.