Both efficient and robust, ROBOTIS Dynamixel servo motors are now being used for prototyping in the field of space robotics, in particular by the French national space agency (CNES).
The CNES is using them for example to design the Earth prototype of an exploration robot to be sent to Phobos, one of the two moons of the planet Mars.
This small robot’s job? To study the physical properties and composition of the regolith covering Phobos’ surface.
Why journey to Phobos?
This rover project sprung from a partnership between France and Germany and is part of the MMX mission (Martian Moons eXploration) headed by the Japanese space agency, JAXA.
The aim of the MMX mission is to understand how the two moons of Mars initially came into being. Studying Mars’ satellites should give us a better grasp of how the planets in the solar system were initially formed, and teach us more about the origin of water on Earth. The Japanese probe will therefore be carrying a multitude of scientific instruments. It will even land on both moons in turn to collect a few grammes of regolith. These samples will then return to Earth in a capsule for research.
The MMX probe will drop the small rover onto the surface of Phobos during a very low altitude flyby. Its mission is then expected to last about 100 days.
These two small moons could be determinant in our conquest of Mars, as they are considered potential relay stations during the interplanetary journey before actually landing. Much like the Apollo module, which served in lunar orbit as a relay station for the Eagle Lander in 1969. The MMX mission is scheduled to be launched in 2024 from the Tanegashima base, and the sample returned to Earth in around 2029.
A Franco-German mission: to design an autonomous rover weighing just 25 kg
The German mission
The German space agency, DLR, is in charge of the rover’s external structure, the components that will make it mobile (legs, wheels) and the mechanism used to separate from the probe. They will also provide two scientific instruments: a radiometer and a Raman spectrometer.
The French mission
The French space agency CNES is developing the on-board computer and its flight software, the power supply (solar panel, battery, converters) and the radio telecommunication link between the rover and the probe. The French instruments consist of four high-resolution cameras.
Mechanical architecture: uprighting
We discussed this mission with Jean Bertrand, an engineer at CNES in charge of mechatronics within the Planetary Exploration Robotics Department at the Toulouse Space Centre.
Jean Bertrand’s role in the MMX mission is to build the Earth model of the rover. And he turned to Génération Robots for motorisation, as France’s exclusive distributor of Dynamixel servo motors.
The purpose of this fully functional model will be to test the uprighting function of the MMX rover.
Why is uprighting important?
When the MMX spacecraft flies over Phobos at a very low altitude (about 40 m), it will simply release the rover, there will be no protection or braking system. Phobos has an extremely low gravity, so a free fall of 40 m is equivalent to a fall of just 6 cm on Earth.
The small rover will then bounce off the surface until it stabilises in a random position. Once the robot is stabilised, the uprighting function can begin.
The robot must perform this critical operation autonomously, as remote control from Earth will be strictly impossible throughout the landing phase. Another constraint is that the operation will have to be carried out with a single battery charge, because at this stage the solar panels will still be folded up on the back of the rover.
The motors will serve to extend the robot’s long legs (with wheels at the ends), which will then act as levers to roll the rover along the ground until it is finally in its operating position, upright on its four wheels.
The uprighting sequence is designed to work regardless of the position in which the robot stabilises on the ground when landing on Phobos. If it falls on its side, the legs will have no leverage. The sequence therefore also includes a “parachute“ position, whereby the rover has all four legs pointing upwards. It is a position that will enable the rover to tip over, at least partially, onto its stomach. Several successive movements of the four legs will then allow it to stand up.
Once it is standing, the solar panels, designed to power the robot throughout its mission, can be safely deployed.
An Earth prototype to test and validate the uprighting function
The prototype used to test and validate this uprighting function will of course be different from the robot sent to Phobos.
The gravity on Phobos is 2,000 times weaker than that on Earth. The real rover, designed for Phobos, could therefore be rapidly destroyed if it were left to roll around in the Earth’s gravity. Its carbon Nida chassis and slender legs (although made of titanium) would not withstand the shocks for very long!
The Earth model must be robust and inexpensive compared to the real Rover. Its virtually unbreakable chassis is made of polycarbonate, and its actuators are Dynamixel servo motors, which are both robust and highly precise.
Advantages of Dynamixel servo motors for the CNES
This project requires use of motors offering different types of control (position and speed). The Dynamixel servos meet these specs, and include precise and stable PID controls.
They also have many configuration parameters. You can easily limit the torque, for example, which is important in ensuring the safety of operators working with powerful servos like the Dynamixel-P. To deploy the legs, the servo torque has thus been limited to 30% above the torque required for the robot to stand.
Another big advantage of Dynamixel servos in respect of this mission is that they can be controlled via a UART serial link. This will also be the case for the robot sent to Phobos, which will use SpaceWire, a computer bus based historically on the IEEE 1355 standard and currently used for many space missions by NASA, ESA and JAXA (the Japanese space agency).
The computer codes used to drive the motors of the model and of the actual rover can therefore be quite similar. Like the DLR locomotion system, the Dynamixel servos can recover instantaneous velocity and instantaneous torque at a frequency of 10 Hz. This is very important, as continuous monitoring of the state of the actuators is crucial for the uprighting algorithm.
Another advantage is that all the servo motors in the range are controlled the same way, making it easy to test several models of servo using the same computer code, and so quickly determine the best servo for a specific application.
It has allowed the CNES team to switch easily throughout the various phases of this project from the mX-64 servos, for the first prototype, to the Dynamixel-P pro range (PH54-100-S500-R) for the final model.
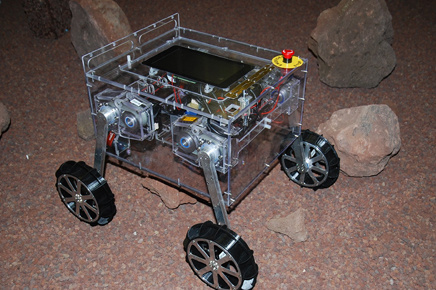
Version of the prototype with MX64-AR servos
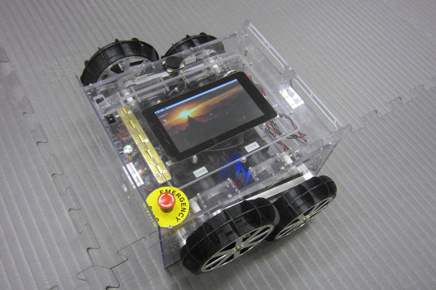
Prototype version with PH54-100-S500-R
The only constraint involved integrating an indexed addressing table into the Dynamixel-P servos so they could be driven using exactly the same computer code as the Dynamixel MX or XM.
In the final version of the model, this mapping table allowed mixed chains between the Dynamixel wheel servos (XM series) and the Dynamixel-P servos (formerly Dynamixel Pro), used to deploy the legs.
The CNES has chosen the C language for the software embedded in the model, again to stick as close as possible to the software used for the real rover. C is not necessarily the easiest choice for driving Dynamixel servo motors, but thanks to the SDK and documentation provided by their manufacturer, ROBOTIS, it is within the reach of C developers who have a few years’ experience.
Dynamixel servo motors chosen for the MMX rover prototype
Wheel drive: XM430-W210-R servos
=> Reason for this choice: While there is no need for a high torque or velocity, size is important, the servos must be compact enough to fit inside the wheels.
Leg deployment: MX-64AR servos, then PH54-100-S500-R
=> Reason for this choice: Initial tests were carried out using the MX-64AR. But in some situations a single servo must be capable of carrying the model’s entire weight, so there was insufficient torque. The Dynamixel-P range of servos provides ample power in all circumstances.