Panda robot arm is the V1 of the Franka Research 3 (FR3) cobot, designed by the German manufacturer FRANKA EMIKA.
The following article reports on an experiment conducted by the Bordeaux – Sud-Ouest INRIA Research Centre, a long-time partner of Génération Robots. In the experiment described below, INRIA researchers used a collaborative robot arm to assist carpenters when milling wood with the aim of reducing (or even eliminating) the risk of accidents.
This article won the Best Paper Award in the Automation category at the ICRA 2020 conference. ICRA is an international conference on robotics and automation. The 2020 edition was replaced by a virtual event (due to the public health crisis) that attracted over 4,000 researchers.
Its workshops, keynotes and plenary sessions were an opportunity for participants to discuss new innovations in robotics, particularly in the context of the fight against coronavirus.
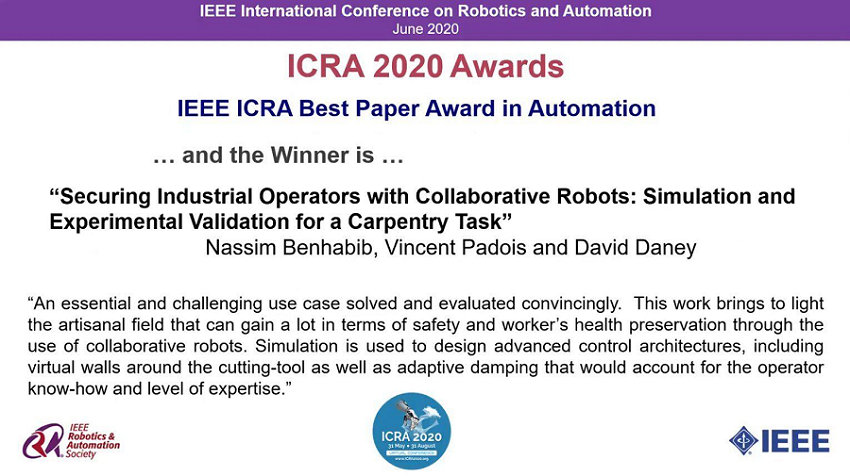
Increasing craftsmen’s safety with collaborative robotics
Aim: reduce (or even eliminate) the risk of accidents for carpenters using table circular saws for board cutting operations.
How: provide craftsmen with a third autonomous robotic arm, whose sole purpose is to ensure their safety.
Carpentry, a risky business
Why milling? The INRIA researchers chose wood milling as their pilot task for this project not only because it’s an essential task in carpentry, but also because it can cause tragic accidents.
In 2016, the French Institute for Craftsmen’s Health and Safety (IRIS-ST) recorded 5,118 accidents for 61,764 carpenters.
27% of them were related to use of tools.
Another study of 1,200 apprentice carpenters found that 80% had already observed a work accident (J. Hester et al.).
Can automating wood milling tasks reduce the risk of accidents?
While automated solutions do exist for milling tasks in industry, for example in metallurgy and for the manufacture of electronic components. these solutions are not adapted to carpentry, which requires flexibility, adaptability and smooth movement.
The existing solutions are also too expensive for small businesses.
This is why collaborative robots is considered to hold potential, since it is less expensive, more flexible, and does not prevent craftsmen from using their know-how.
Alternatives to collaborative robot arms have also been considered for assisting carpenters and improving their safety. For example an exoskeleton designed to give operators more strength, thus reducing the risk of accidents associated with fatigue and strenuous tasks.
Experimental use of a collaborative robot arm for cutting boards
The robotic arm used in the experiment described below is the Panda robot manufactured by the German company FRANKA EMIKA, distributed in France by Génération Robots.
Panda is a robotic arm of excellent manufacture. It has 7 degrees of freedom and is ROS compatible.
It has torque sensors in all its axes for a very high level of compliance, particularly important in this context.
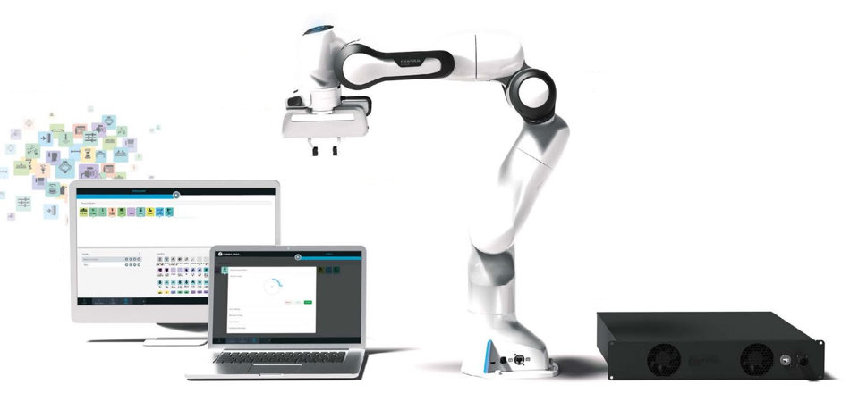
Panda is also less expensive than other similar collaborative robot arms, and has technical specifications ideally suited to this experiment.
If you’re looking for a robot arm for your own project, we suggest you read our helpful “Criteria to look at before buying a robot arm” article.
Purpose of the collaborative robot arm
Wood milling accidents occur mainly when the saw blade hits a knot in the wood. This abruptly changes the pushing parameters (speed/direction) and surprises the operator.
A collaborative robot arm can therefore act as a safeguard for craftsmen. It would allow them to continue cutting boards, sliding them over the table towards the circular saw, with the robot arm assisting their movement. The arm would immediately detect a change in board speed or direction, and compensate for this change by instantly adjusting the pushing force.
With this system, operators should no longer see any sudden changes in the speed at which boards slide, thus greatly reducing the risk of accidents.
The advantage of this solution is that the machine is simply assisting the person, not replacing them. Craftsmen remain in full control of cutting and in contact with the material they are working on.
Stage 1 of the experiment: create a model
The research team began by creating a virtual model of a circular saw mounted on a table, accompanied by a human operator. This model was then transferred to MATLAB.
During the simulation, various parameters could be modified, including the pushing force, the thickness of the board, the presence and location of knots in the wood, and the speed of rotation of the saw.
The researchers were able to use this virtual model to run and study simulations of various scenarios potentially dangerous for operators and likely to lead to an accident.
The model could create numerous milling simulations, both optimal and sources of accidents.
Stage 2 of the experiment: reproduce the simulation in real-life conditions
Construction of the model
The team designed an experiment to confirm the observations made during the simulation on the effects of a sudden change in cutting speed.
To avoid unnecessary accidents, the Bordeaux – Sud-Ouest INRIA research team thought it would be safer to create a mock-up cutting table, consisting of a guide rail mounted on a table along which a board could slide. A FRANKA EMIKA Panda robot arm was then added to complete the set up.

A counterweight system positioned beneath the table allowed the researchers to adjust the sliding speed of the board to match that of a cutting table.
Real-life testing
The research team asked three different people to simulate board cutting using this model. Each performed five tests, the results for which were measured and recorded. Prior to these tests, the three subjects could first perform a few trials to familiarise themselves with the set up and with the movements performed.
In the course of the various tests, the researchers simulated the appearance of a knot, causing a sudden change in speed.
For subject 3, the Panda robot arm applied an additional downwards constant vertical force of 50N (when the rate of change of the planar velocity was greater than 20m/s²) while sliding the board through the knot.
The following curves show the three scenarios induced when simulating a knot in the wood:
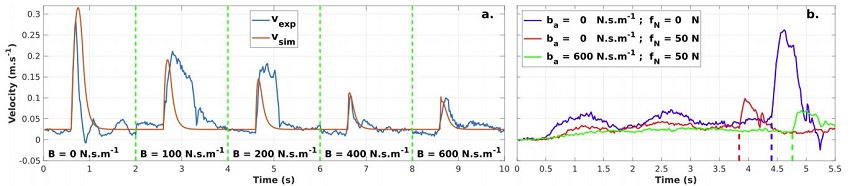
- Scenario 1: without the robot (blue curve)
- Scenario 2: the robot applies a constant vertical force (red curve)
- Scenario 3: the robot applies a constant vertical force (braking action) and at the same time a maximum horizontal damping action (green curve)
Conclusions
Ideally, further comparison and optimisation of scenarios 2 and 3 (see above) are needed.
The promising results show how simulation can be used as a tool for designing advanced control architectures. It would be worthwhile improving the virtual model, notably by taking into account the know-how and level of expertise of the virtual carpenter, which are factors that should not be neglected.
Overall, based on this research, the artisanal sector clearly has a lot to gain from using collaborative robots in terms of safety and accident prevention.
You can read the article published by the research team here: Securing Industrial Operators with Collaborative Robots: Simulation and Experimental Validation for a Carpentry task
Integration of 4 cobots setup on a telescopic column, mounted on omnidirectional mobile robots
Assistant robots designed to help with household chores (especially for the elderly or people with reduced mobility) is an issue that many researchers are working on.
It is in this context that the University of Freiburg
(Albert-Ludwigs-Universität Freiburg) asked us to provide them with 4 semi-autonomous robotic platforms.
Download the Franka Emika user guide
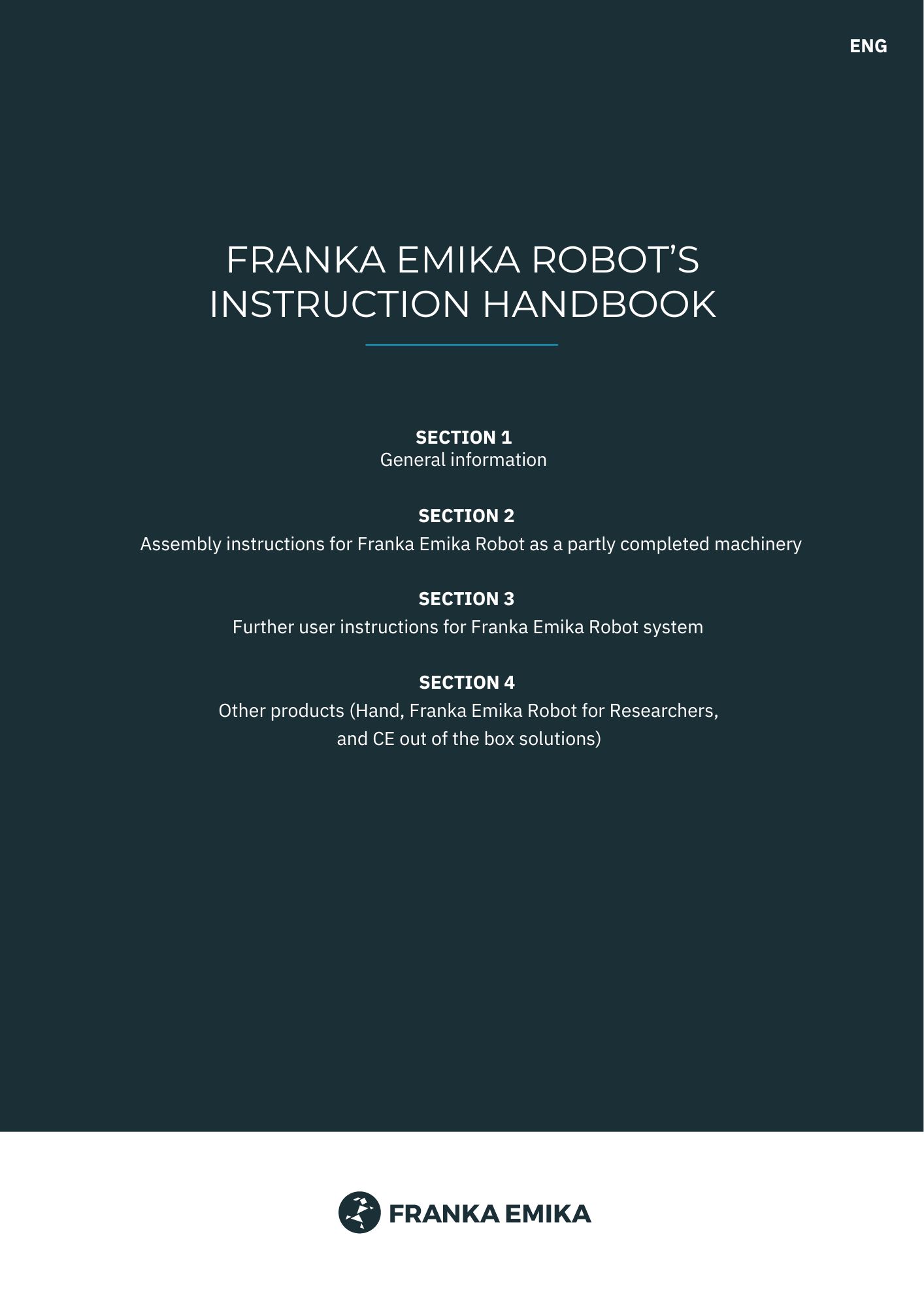