Obtaining the maximum amount of data about an environment is a perpetual quest in robotics. Measuring distances is a fundamental component of this data.
Ultrasound sensors are very commonly used to measure distance because they are inexpensive and easy to handle. They are also used to avoid obstacles, to navigate, and for what is known as map building.
This article focuses on this technology, its benefits and limitations, how it is used and what the differences are between the sensors on offer.
The different ways of determining position of a robot using a signal
Before examining ultrasound sensors more closely, let’s see what other technologies are available. All sensors make it possible to gain a picture of the environment (contact, odometry, sensitivity to light, to sound, to heat, etc.). Some sensors can be used to measure the distance of obstacles, and consequently enable a robot to take a decision depending on the obstacles, or lack of obstacles, around it. This is referred to as range finding , i.e. measuring the distance of a remote point.
Discover our laser ranger finders
- HOKUYO Laser range-finders
- SICK Laser range-finders
- YDLIDAR Laser ranger-finders
- ROBOSENSE Laser ranger-finders
- OUSTER Laser ranger-finders
Besides ultrasounds, three other range-finding technologies are used to carry out such measurements:
- Infrared
- Laser
- Time of Flight (TOF)
The following table introduces the main advantages and disadvantages of the various options in terms of the solutions offered by mobile robot manufacturers as shown on this website.
Ultrasonic sensor | Infrared | Laser | Time of Flight (TOF) | |
Range | From 1 to 250 cm | From 5 to 80 cm | Several metres to tens of metres depending on the model. | 20 cm-14 m indoors (5/6 m in sunlight) |
Directivity | Cone of approx. 30° | Cone of approx. 5° | The most directional (around one degree, or even half a degree). | Cone of approx. 3° |
Accuracy | Relatively accurate but accuracy lessens with distance, with the measurement angle and with temperature and pressure conditions. | Relatively accurate but accuracy lessens over distance. | Accurate to within a few centimetres over measurements of several metres. | ± 4cm in precision mode |
Cost | Inexpensive | Inexpensive | Relatively expensive | Inexpensive |
Sensibility to interference | Sensitive to temperature and pressure. Also sensitive to other robots using the same frequency, which can cause problems in competition. | Sensitive to strong light sources containing a high level of infrared radiation, and also to the colour and type of obstacles. | Cannot detect objects that reflect lasers (windows, chrome-plated objects, etc.). | Can be used in a wide variety of environments and on most materials and surfaces. |
Ultrasound
Sound and ultrasound
Sound is a mechanical, elastic wave spreading through a physical medium in the form of longitudinal or compressional waves. This phenomenon is, for example, put to good use by loudspeakers, which cause a membrane to vibrate, which in turn causes the air to vibrate. Sound spreads more quickly the denser the environment, which explains why sound travels faster underwater than in the air. It also explains why ultrasonic sensors do not work in a vacuum, because sound waves cannot travel in a vacuum. You will therefore never see ultrasonic sensors on space probes or lunar rovers.
Ultrasound has a frequency of over 20,000 Hz and is therefore inaudible to humans (hence its name).
There are two types of ultrasound, depending on frequency range:
- Low-power ultrasound, which is used for measuring distance (range finding), non-destructive tests, echography (ultrasound scanning) and sub-marine acoustics. This is the type of ultrasound of interest to us here; and
- High-power ultrasound, which changes the environment within which it spreads. Its effect depends on the medium through which it is travelling, and may be mechanical, thermal or chemical.
Ultrasound in nature
Many animals can hear ultrasound, such as dogs and bats. Bats also have the special ability to emit ultrasound for the purposes of finding their way around, known as echolocation. This is exactly the principle used by the robots we program. Other animals have this faculty (whales, dolphins, chiroptera (bat family) and some rodents). They use ultrasound not only for finding their way around, but also to pinpoint prey and to communicate.
Information Society Technologies created the Bat-Bot robot in order to better understand the echolocation process. In fact, while echolocation in water is well-understood through sonar, it is much less so in air. The aim of the CIRCE project conducted by Antwerp University is to better understand these phenomena and make it possible to then offer much more advanced and effective ultrasonic sensors than those currently found on the market. In fact, as we will see later, these sensors are quick and easy to use, but problems do arise as the environment gets more complex. |
Humans have put echolocation to good use in various fields. One of the best-known is the ultrasound scan, which can be used to see certain living tissues working (for example, a foetus in a mother’s womb or joint ligaments). The other well-known use is sonar, used by military ships and submarines.
Ultrasound sensors for mobile robots
Ultrasound sensors work by measuring the return time of a sound wave – inaudible to the human ear – emitted by the sensor (transceiver). As the speed of sound is essentially stable, the obstacle’s distance can then be deduced.
Physical and technical properties of ultrasound sensors
The sensors supplied often take the form of a pair of eyes, because there are two key parts:
- The transmitter
- The receiver
The transmitter emits a sound at a defined frequency (typically around 40 kHz) and the receiver collects the sound reflected back by obstacles. Distance to objects is calculated by measuring the time taken by the sound to return to the receiver.
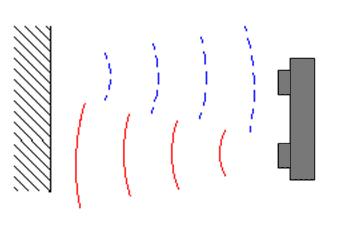
The shape of the beam is characteristic of the sensor used. Figure 1 shows a typical shape for an ultrasonic beam.
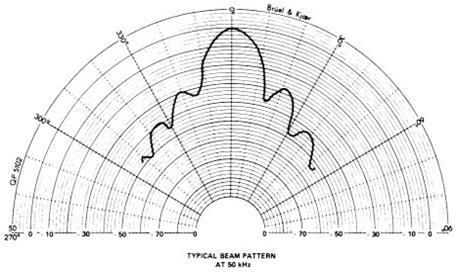
Note that the effective working angle is approximately 30° (which is large compared with other types of sensor), with smaller secondary lobes on each side. Measurement will consequently be more accurate within the central cone of 30°, and less accurate towards the sides. This explains why ultrasound sensors are typically mounted on rotating components so that different measurements can be taken using the central section of the viewing cone.
The width of this cone (30°) is both an advantage and a disadvantage. It is a disadvantage because any obstacle detected is not located precisely within the detection cone. Measurement of position is therefore relatively imprecise. It is, in contrast, an advantage in that it enables the environment to be scanned more effectively, and narrower objects, such as chair legs, will definitely be detected.
The diagram below shows three typical measurement scenarios.
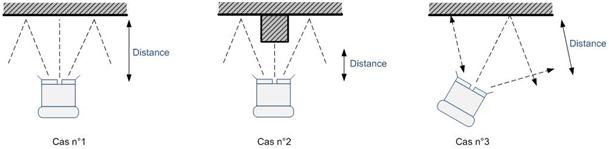
The first scenario will generate a precise measurement because the ultrasound sensor is opposite and perpendicular to the obstacle.
The second scenario will also generate a precise measurement, but will give a “view” of the obstacle located directly opposite the ultrasound sensor.
The third scenario will generate an inaccurate measurement however, given that it is the left side of the ultrasound sensor that is taking the measurement.
It is essential to properly understand the beam structure for the ultrasound sensor being used if it is intended for map building. This is less true for obstacle avoidance.
The fact that ultrasonic sensors are blind at very short distances also needs to be taken into account. This is because of the time delay between emitting the ultrasonic wave and the start of detecting the reflected wave, which is necessary so as not to interfere with measuring.
Some limitations of ultrasound sensors for robots
The shape of obstacles plays an essential role, because it may cause the robot to incorrectly visualise its environment.
> Obstacle shape
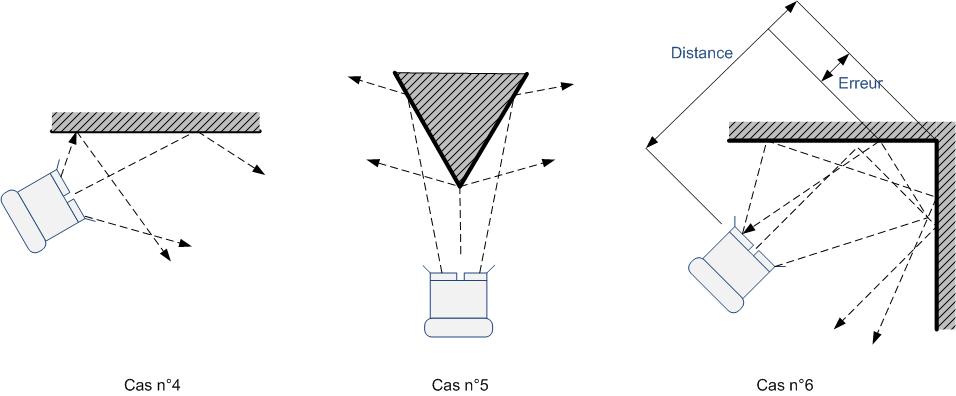
As the figure above shows, errors generated by obstacle shapes have to be taken into consideration.
> Obstacle texture
Texture also plays an important role. A carpeted wall will reflect waves less well than a painted wall.
> Cross-talk
Two ultrasound sensors cannot be used side by side because if they use the same frequency it is not possible to distinguish which one has emitted a wave. This is referred to as cross-talk.
Another solution for a robot that has more than one ultrasound sensor is to activate them one after the other, which reduces the overall refresh rate.
> Perceptual aliasing
Among the other types of limitation worth mentioning is the problem of perceptual aliasing. This problem arises when a robot is confronted with ambiguous situations that prevent it from choosing with any certainty the most appropriate action, because it lacks enough data about the environment. For example, while an ultrasound sensor enables a robot to position itself alongside a wall, it doesn’t usually enable the robot to know where it is located along the wall – is it at the start, middle or end? Two measurements taken at any point along a wall will provide the same information (unless the robot reaches the end and it detects the absence or presence of a corner).
This problem therefore refers to a sensor’s inability to differentiate between all the different locations within an environment.
To circumvent this problem, several algorithms are possible: learning-based algorithms, memory algorithms, etc.
The way the robot is programmed is an effective way of minimising these side effects, as is increasing the number of sensors.
Examples of ultrasound sensor implementation in robotics
The following are some videos showing examples of ultrasound sensor use.
Obstacle avoidance
In this video, the robot heads towards the most open area. The Boe-Bot kit was used here.
Radar
Here, the designer has programmed the robot so that it is static, but uses the ultrasound sensor as radar. It displays the objects it encounters on the screen of the EV3 intelligent brick.
The various ultrasound sensors
We will concentrate here on the ultrasound sensors offered within the robot ranges offered by Generation Robots .
Lego Mindstorms EV3
![]() |
This ultrasound sensor is included in the Lego Mindstorms EV3 kit.
The product’s official specifications are as follows:
|
The few limitations that have emerged with this ultrasound sensor are:
- Measurements under 4 cm cannot be made. This is because of the return time needed for the wave;
- Measurements up to 20 cm are relatively accurate within an angle ranging between -8° and +30°. In fact, the receiver is on the left and the transmitter on the right, which explains why measurements made on the left are less accurate than measurements made on the right; and
- Between 20 and 80 cm, measurements can still be made with a margin of error under 8%, which is not too bad for a sensor of this kind.
The improvement of the ultrasonic EV3 sensors are:
- A detection range between 1 and 3cm
- Can be used as a sonar
Grove Ultrasonic Ranger
![]() |
Grove Ultrasonic Ranger can be connected to
your Arduino
via a Grove board for easy prototyping. This ultrasonic Grove sensor is capable of guaranteeing you industrial-level performance: a range of 3 cm to 4 m, with a resolution of 1 cm.
|
HC-SR04 ultrsonic sensor: high precision with a low cost
![]() |
The HC-SR04 ultrasonic sensor is a popular choice for prototyping. Easy to use with an Arduino and compatible with Raspberry Pi , its scanning range is pretty good, with stable measurements and high precision for an inexpensive ultrasonic sensor (3,95€). |
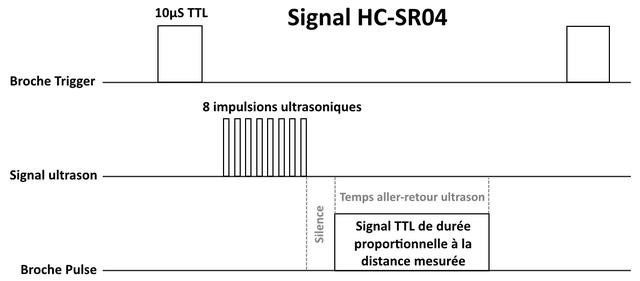
- Measuring angle: <15°
- Ranging distance: 2cm – 500 cm
- Resolution: 1cm
- Ultrasonic Frequency: 40k Hz
TeraRanger Duo distance sensor: TOF + ultrasonic
![]() |
If you’re not yet familiar with ToF technology, bear with us: a ToF distance sensor emits a flash of light with a photodiode and calculates the time needed for this flash to reach a target object then return to the sensor. The sensor/target distance is calculated automatically based on the time of flight.
The TeraRanger Duo distance sensor combines 2 technologies, thus offering an excellent detection precision, regardless of the terrain on which your creation has adventured; whether navigating a carpet, a glass surface or even a small body of water, nothing will escape its expert eye. Time-of-flight technology offers an excellent update rate, a long range and record accuracy, while ultrasonic technology gives a wider detection angle. Combine the two and you get a highly reliable distance sensor in a compact, lightweight format.. |
Vex Robotics
![]() |
This ultrasound sensor is not included in the basic kit but is available separately.
This sensor’s technical specifications are as follows:
|
This ultrasound sensor requires the RobotC programming kit, which is included within the VEX Robotics kits sold on Generation Robots .
An example of using the ultrasound sensor with a Vex robot:
Parallax
![]() |
This ultrasound sensor is not included in the basic kit but is available separately. It is adaptable both for Boe-Bots and Sumobots.
This product’s technical specifications are as follows:
|
The transmitter is on the right and the receiver on the left when looking at the sensor head on (as shown in the figure below).
Conclusion
Ultrasonic sensors are easy to configure and, when combined with other sensors, enable very useful data to be provided about the robot’s environment. Your robots will no doubt have one or more sensors of this type!
Generation Robots ( https://www.generationrobots.com/en )
All use and reproduction subject to explicit prior authorization.